Thornthwaite is a long-established washroom technology business, with an experienced and friendly team with representation across Australia. We've been operating since 1933 and have built our reputation on great customer service, advice and products.
Our Managing Director is Andrew Thornthwaite, grandson of the founder of our business, HG Thornthwaite. Andrew took over the business in 2003 and since then has sought to constantly improve our product lines, business processes and customer satisfaction.
For more information about us, visit our About Us page
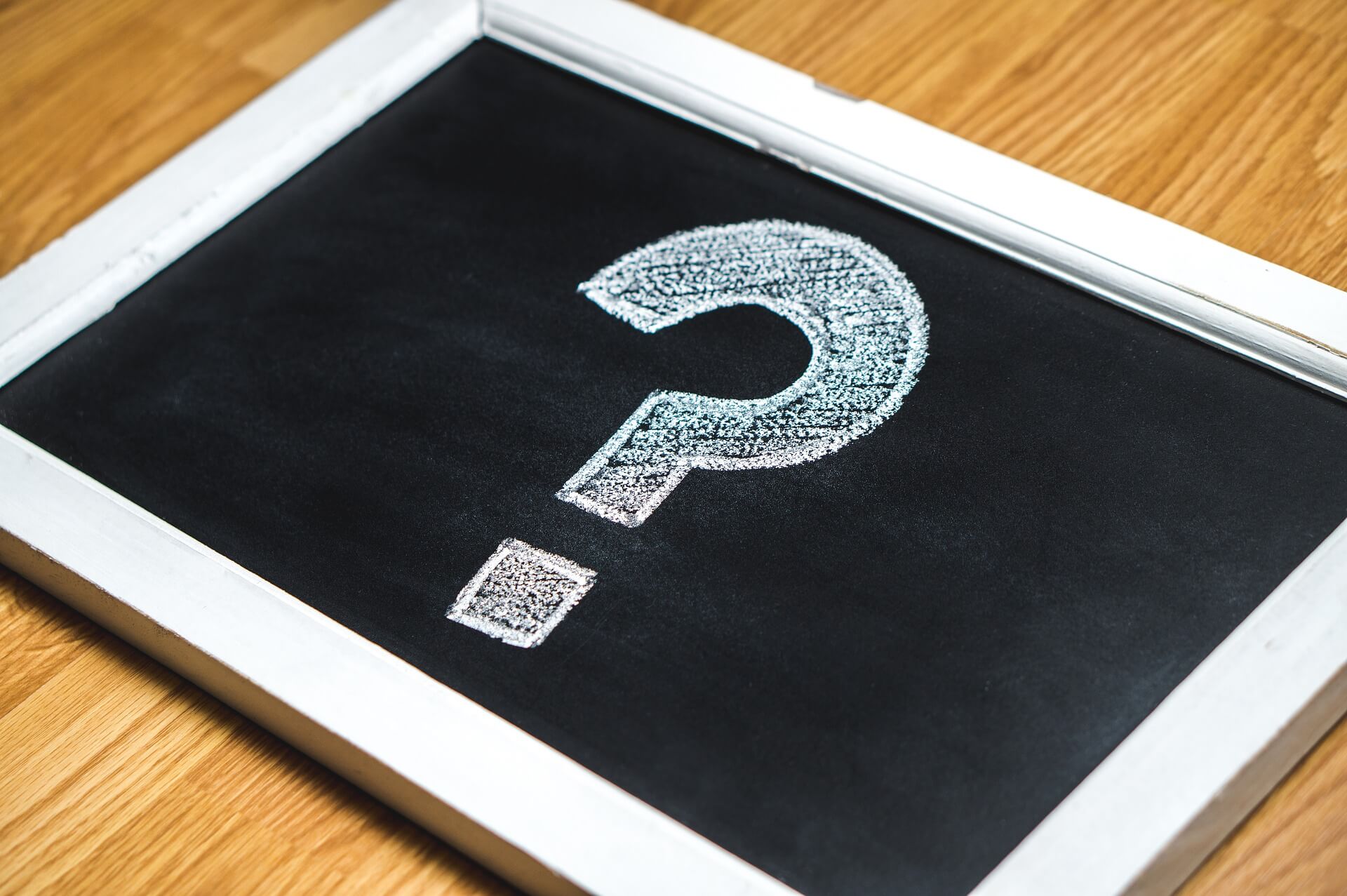
AUSTRALIAN STANDARDS
Yes, it is mandatory.
The tap will be marked with a sticker or alternatively embossed or stamped with the WaterMark Logo and the relevant Licence number.
Australian Standard AS/NZS 3718 tests the materials used to construct tap ware to ensure that carcinogens, chemicals or harmful metals such as lead will not contaminate water passing through the tap (refer to AS 4020). This standard also ensures that the clarity and taste of water will be to acceptable standards.
The approval process for AS/NZS 3718 includes testing that all tapware is manufactured with dezincification-resistant brass (DR brass, refer: AS2345). This ensures that the water supplied to the tap will not corrode the brass body.
If tap ware is approved to AS/NZS 3718, then the pipe threads conform to the relevant Australian Standard. This ensures that the connections to the pipe work can be sealed with ease, avoiding any leaking problems in the future.
PRESTO TAPWARE
Many of the taps in our Presto range have a security option, which makes them ideal for areas where wasting water is a problem.
Our standard versions allow the user to press the push button and water automatically flows. In our security version, the user must push and release to activate the water flow.
Both versions feature timed flow, automatic shut-off and low flow rates.
Yes, we have Presto Volta sensor taps, as well as Rada Pulse and Mono (sensors for basins, showers and urinals) and Rada Sense (sensors for basins and showers).
RADA SHOWERHEADS
VR stands for vandal resistant.
Rada's vandal resistant shower heads are made from strong and solid chrome plated brass. When installed they are well secured to the wall by a mounting plate and a barrel nipple which connects the mounting plate to the water supply. The shower head itself then plugs onto the secure mounting and is retained. The showers are supplied with a strainer screen and a flow regulator, both located within the body of the shower and are not accessible to users of the shower.
RADA PULSE & MONO CONTROL
Rada Pulse and Rada Mono Control are sensor-based washroom controls. Rada Pulse can control up to 10 outlets via a single control box. This could include a mix of basins, showers and urinals, all of which can be programmed via a hand held programming unit. To install Rada Pulse, you'll need up to 10 sensor kits (including a sensor and solenoid valve), a Control Box and a handheld programmer. Mono Control on the other hand is a self-contained kit for a single outlet. The sensor kit comes supplied with everything you need as a single part number, including the sensor, solenoid valve, a control module and a plastic enclosure. Each outlet is programmed using the control module.
The Rada Pulse Control Box has three additional sets of terminals which can be connected to three 12VAC to 240VAC relays which are mounted in the one assembly. These relays can be individually connected to a pump, light or exhaust fan. The Rada Pulse system can then be programmed to allow any of these auxiliary pieces of equipment to operated when a predetermined number of sensors have been activated.
PRESTO VALVES
We recommend our Presto 712 S Knee valve which must be activated and released before the water starts to flow. If the lever is held in the activated position no water will flow, so the end user is then forced to release the lever before receiving approx 15 seconds of water flow. With the standard version of the Presto 712 knee valve it is possible to hold or tie the lever into a position so as to obtain a continuous flow of water and then once the lever is released the flow will shut off in approx 15 seconds.
RADA MIXING VALVES
Radatherm is sealed-for-life thermostatic cartridge used in Rada mixing valves.
Therefore, it dramatically reduces the service time required for maintenance compared to traditional TMVs. Under normal circumstances does not need to be removed every 12 months, however should be replaced every 5 years.
For optimal performance. Radatherm should be inspected at least every 12 months, to clean or replace the strainer screens and verify that the mixing valve is open correctly.
The following models incorporate the Radatherm cartridge:
- Rada 215bk
- Rada 215dk, Rada 215oemk and Rada 215zk
- All Rada 320 variants
Read more about the Radatherm features and benefits.
Changing the Radatherm cartridge should take approximately 10 minutes, following these instructions.
Remove the white locking cap by unscrewing the allen screw located at the centre of the cap and lift the white cap away from the valve.
Do not remove the black plastic circlip from the head nut.
Using an adjustable spanner unscrew the the large brass hexagon nut until the thread is disengaged from the body of the valve making sure to leave the black plastic circlip in place. Once the the head nut is disengaged pull the head nut and cartridge from within the body of the valve. Now remove the back plastic circlip from the head nut and remove the head nut from the old cartridge.
Select the new replacement cartridge (part numbers 40899 for 215, 41451 for 320) and fit the existing brass head nut and the black plastic circlip to the new cartridge. Then push the new cartridge into the body of the valve making sure that the inlet cartridge O-rings are greased and are orientated so that when the cartridge is pushed into the valve they are not directly over the square cut-outs.
Once the cartridge has been pushed in, it can then be realigned so that the relevant inlet ports of the cartridge and the body of the valve are correct. When in the correct position, screw the brass head nut until tight. Replace the white locking cap and return the valve into service.
RADA SENSE
A digital mixing valve is a thermostatic mixing valve (TMV) that is digitally controlled and incorporates a sensor to enable a user to turn a basin or shower on/off as well as adjust the temperature. It uses two temperature probes to detect the temperature of the mixed water flowing from the valve and transfers this information via Rada's T- Logic digital intelligence to a small stepper motor which adjusts the temperature control mechanism to maintain the desired mixed water temperature.
Rada Sense has a factory pre-set maximum temperature of 41°C. The person using the basin or shower is able to adjust the temperature from full cold and from 30°C to 41°C via the sensor control. If other temperatures are required for the application, a qualified plumber (with a PDA, Rada Sense software and login passwords) can adjust the programmable settings to the following: Max. 33 - 50 °C; Min. 30 - 47 °C (full cold can be disabled if required); Default at start-up 30 - 50 °C.
RADA LIGATURE RESISTANT
The Rada LR showerhead and Rada LR Spout are identical in shape. They are curved so as no matter how a ligature is tied to the shower head / spout the ligature will slip off.
The shower head can be used as a spout by reducing the flow rate through the fitting to 5 L / min.
The LR Sensor must be used in conjunction with the Rada Pulse operating system.
SPECIFICATIONS AND TECHNICAL SUPPORT
First of all, this website will provide you with information about products, downloadable datasheets and line drawings, and product manuals. If you would prefer to handle the products and see the quality for yourself then our Sales & Specification Consultants are available for on-site appointments to demonstrate our products, discuss your specific project needs and recommend the best products for your build.
You can contact our team directly or use our contact form to get in touch.
Our Sales and Specification consultants can usually resolve technical issues over the phone or can arrange an on-site visit. Alternatively, call our technical support team on 02 9417 4466 and they will be able to help you.